Phase 1: Rapid Response and Initial Reset
Step 2: Safety, Spatial Awareness and Human Work 2
People, Behaviour and Poka-Yoke Thinking
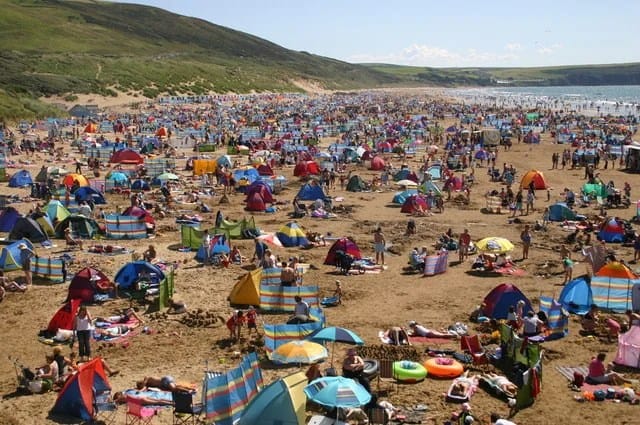
A crowded beach and the desire for social distancing is hard to maintain. How do you control “contact” and possible transmission? As restrictions ease the number of contacts and nature of those contacts will change. Managing workplace safety through work design will be key. Do we trust in common sense or do we do as they did in France where they shut the beaches and fined many people?
Poka-Yoke Thinking and the Risk of Transmission
Human beings and our behaviour and choices are at the very heart of this awful pandemic. Although initially caused by a virus the infectious disease it starts is contagious and can readily be transmitted from human to human. The virus is not a living thing and it is, therefore, propagated and transmitted by us humans and our activities. Anything that we can do to reduce or halt that transmission is critical. However, it isn’t as easy as it initially sounds.
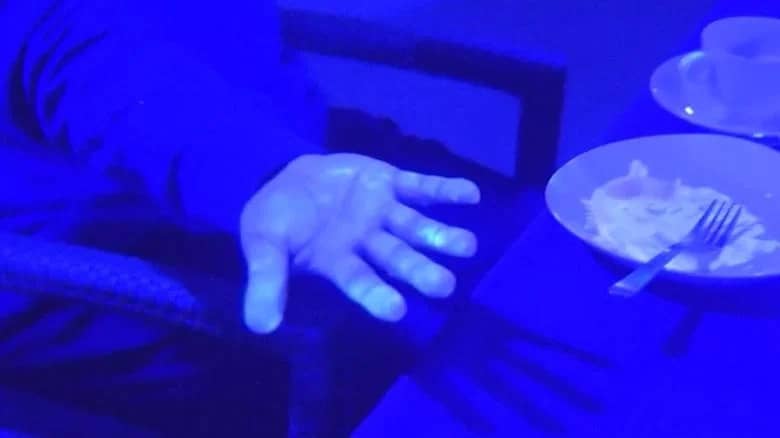
In May a Japanese public broadcasting organisation NHK, in conjunction with health experts, set up a black light experiment to show the possible extent of germ transmission within a simulated environment https://edition.cnn.com/2020/05/13/health/japan-black-light-experiment-coronavirus-trnd-wellness/index.html. They setup a “fake” buffet restaurant with 10 customers and they applied a fluorescent substance, only visible under black light, to one customer’s hands to simulate a “germ”. After a 30 minute period they turned the black light on to find out the extent of the transmission. The “germ” had been transferred to all 10 customers and traces can be seen on hands, clothes, faces, tongs and containers. It is a sobering watch.
The BBC ran an article that showed a similar experiment, “watch how germs spread” but, this time in lab conditions at the University of Westminster. https://www.bbc.co.uk/news/av/health-51637561/coronavirus-watch-how-germs-spread If transmission is what we want to eradicate or minimise how do we go about it? Poka-Yoke thinking can help here.
Poka-Yoke and the Importance of the “Human Element”
Toyota in the UK describe Poka-Yoke as “Poka-Yoke (English: mistake-proofing): Fail safe devices in the production process that automatically stop the line in case of an error. A Poka-Yoke is any part of a manufacturing process that helps a Toyota member avoid (yokeru) mistakes (poka)” https://blog.toyota.co.uk/poka-yoke#:~:text=Poka%2DYoke%20(English%3A%20mistake,yokeru)%20mistakes%20(poka). In his infamous blog Michel Baudin is more explicit about the human element saying “A Poka-yoke is a device integrated in a manufacturing operation to prevent human error. As an approach to quality improvement, it is therefore relevant where human error is the main cause of defects.” https://michelbaudin.com/2013/08/08/more-on-poka-yoke/ The subtle understanding of human behaviour is closely tied to the success of a Poka-Yoke as Michel Baudin goes on to explain, “one feature of Poka-Yoke that is often missing in the literature is that the defect-prevention devices must not add labour. The reason this is vital is that, otherwise, operators will stop using them under pressure and they will be ineffective. For example, validating picks by reading bar codes adds labour if an operator has to wave a reader and is therefore not a Poka-Yoke. If the ID Is read automatically while the part travels on a belt, then it is a Poka-Yoke.” In fact, at the heart of Poka-Yoke thinking is the reality that human beings do often make mistakes for many and varied reasons.
TO ERR IS HUMAN – “Poka-Yoke is NO Joke”
One thing that Shigeo Shingo found when endeavouring to improve quality as an industrial engineer was that even if a process was “capable” the system could still produce defects. This is because as humans within complex systems we will make mistakes. The systems, policies, demand pressures, usability of the human/machine interfaces all contrive to ensure it happens. Once you accept that humans will make mistakes then you are in a position to start to analyse, review and do something about it. That thinking is at the heart of Poka-Yoke. The adoption of Poka-Yoke thinking in healthcare can and is making a difference. In 1999 in the US the Institute of Medicine published a landmark report called “To Err is Human” which highlighted the mortality rate that could be attributed to mistakes and how this number could be dramatically reduced. This same report is highlighted in the 2010 Harvard Business Review article “Poka-Yoke is No Joke” by Michael Schrage https://hbr.org/2010/02/my-favorite-anecdote-about-des.html It is also covered in Mark Gaban’s well-known lean healthcare blog #329 in which he interviews filmmaker Mike Eisenberg who made a film about patient safety based on landmark report https://www.leanblog.org/2019/01/podcast-329-mike-eisenberg-the-film-to-err-is-human/ Using the same thinking can help to design and fashion safer workplaces and environments.

If it is proven that humans will inadvertently make mistakes then we need to ensure that any countermeasures to “contact” are robust and reflect our human frailties. When designing workplaces and environments it is important to understand that reminders, training and signs are simply not robust enough to prevent humans doing the wrong thing. The countermeasure ladder or the Miliken countermeasure ladder as it is sometimes referred to is a good tool to judge the strength and effectiveness of your chosen solutions. Above level 4 and you are acknowledging that to err is human and that an error is not the same as an abnormality.
Errors and Defects are not the Same
Because we are concerned with human error when we are thinking about Poka-Yoke we need to understand the difference between the error and the result. In a manufacturing process if I miss a step out it could result in me making a defective part. In that case the error and the result are clear and the product may be scrapped. When using this analogy within safe workplace design we could work backwards from the result we don’t want to determine the potential errors. The result we don’t want is transmission of the virus via some type of contact. From that point we can then start to work back and list all the errors that could cause the contact. This is what the black light experiment so clearly shows us.
Obviously, it would be best if we could eliminate all possibility of contact as then there would be no human error and possible subsequent transmission. Working from home certainly helps with this.
Prevention Not Cure is Key (as there is NO Cure)

However, zero contact is unrealistic so we need to design our workplaces by imagining that we have fluorescent paint on our hands or think of ourselves as infected and contagious. In manufacturing, Poka-Yoke is seen as a zero defect approach as it goes to the source to ensure errors never result in defects. If we eliminate, control and contain errors they never progress to result in a defect. If an error occurs then it is highlighted and communicated immediately. Therefore, if contact is an “error” we need to be able to control and contain it through PPE, bubbles, “households”, zero sharing and sympathetic workplace and environment design. It is also vital that if someone believes an uncontrolled contact occurs they immediately communicate it. The figure above links the previous countermeasure ladder to the flow of a step, task or activity. It has been developed based on a Takeshi Nakajo attributed figure in a ASQ paper about healthcare focused error proofing “Healthcare-Focused Error Proofing: Principles and Solution Directions for Reducing Human Errors
By Blanton Godfrey, Timothy G. Clapp, Takeshi Nakajo, Chad S. Seastrunk”. The logic is that with a traditional or typical application of a Poka-Yoke you are able to contain the error and either not make the defect or immediately stop it progressing. However, if the error is a unplanned “contact” then without immediate handwashing all the other containment strategies are required.
So the logic of Poka-Yoke thinking and the pragmatic understanding of human behaviour would mean that you eliminate the need for contact outside of your household, you do things online that you would normally do in person and you design work and workplaces that minimise contact within bubbles. If you are in any doubt just keep viewing the black light fluorescent dye experiment and you will see how easily the “germ” is transferred.