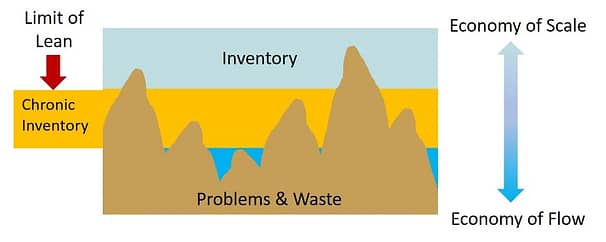
Almost Lean but Without the Real and Profound Benefits
When the counter-intuitive reveals itself it generates a feeling like no other. As many say it seems like a veil is lifted and our mental “blinkers” are removed. That moment of knowledge, when an idea or problem finally make sense is satisfying, exhilarating and frightening. At the heart of TPS and lean is the concept of flow and the elimination of unnecessary activity. The “sell one make one” concept drives alignment and synchronisation with your customer or user. However, it is a stark reality that many advocates, supporters and practitioners of lean haven’t and many may never experience the profound counter-intuitive impact of these principles on an organisation. This reality comes about because of the self-limiting level of chronic inventory or work always in the system whether material in a plant or knowledge work. It stops and will always prevent organisations experiencing the profound power of the economies of flow. It is severely limiting because the economies of flow deliver an exponential level of possible competitive edge benefits for both the soft and hard aspects of a lean system. It is a chronic level and problem because it is always there; lived-with, assumed, on-going and ignored. Almost lean but without the real and profound benefits.
Overreaction to a Probable Swiss Cheese Event
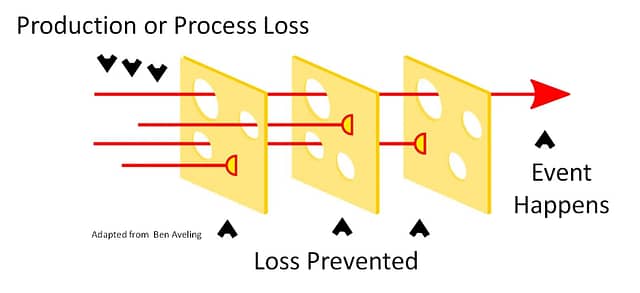
The fuss and exposure afforded the recent Google outage reminded me of the situation in many plants and organisations I have visited over the years. I can only be thankful for the efforts of the Google staff behind the scenes that quickly dealt with the 0.05% event and thereby keeping my service uptime at 99.95%. However, all too often the leadership and management reaction to a sporadic, random, unpredictable outage or stop far outweighs the real impact of the actual event. The crisis team then try to carry on to investigate, study and analyse a rapidly cooling trail of leads from a Swiss cheese event that may never occur again. This generates more heat than light and often diverts attention away from the real problems and issues that are common and baked-into the current process and equipment. Whilst overreacting to that situation they ignore the constant common cause loss right in front of their eyes.
Living in the Shadow of Chronic Losses – Our Constant Blind Spot

Imagine one day you decide to slow some equipment on the line down by 10% to notionally overcome a minor stops issue. This inadvertently becomes the normal, accepted speed. Imagine you decide to temporarily extend the calibration frequency of the weigh scales and they drift off and start to accept giveaway. Imagine you decide to start some more user stories or features on the backlog to keep the team “busy”and it becomes accepted. All these situations are all entirely plausible. Often the reality is there are cumulatively massive chronic losses or issues we just go on accepting as “everyday”. This “common cause” loss can be accepted and we become blind to it. However, it can actually be our greatest source of improvement but we, all too often, get distracted by the shiny thing we see or that management focus on instead. Invariably a creeping, quiet level of loss increases, unchallenged. That is what also happens with inventory.
Quantifying the Lost Economies of Flow
The impact on flow of a chronic level of accepted inventory is hard to articulate to someone who hasn’t been lucky enough to go through the normative experience of working in a very small batch, pull system environment, it’s counter-intuitive. The level of inventory or work to be done is often accepted and we just try to implement as much lean as we can around it. However, it keeps us away from our customers. It ties up cash or value generation. It slows feedback and response times. It separates teams and processes. It adds massive amounts of secondary unnecessary work. It generates multi-tasking. It needs managing, prioritising, planning and organising by planners or product owners………the list is almost endless. Although our original goal may have been to become “lean” in reality through policy decisions and an acceptance of traditional thinking we never truly expose the rocks and see the economies of flow. However, all is not lost as there are tell-tale signs that you have a chronic level of inventory or work in the system and there are ways to eradicate it.
Spotting and Eradicating the Chronic Inventory

There is very often a mis-match between the concept or principle of lean and the reality of it’s application. The reality of it’s application is that organisations are often left with the legacy of chronic inventory or work in the system. My friend and colleague John Darlington says that “inventory is capacity in the bag” and “inventory is an intermediary between demand and capacity. You can use it to assess how well you have used your precious capacity”. When you really examine the inventory or work you have you can determine why it was produced or launched. For example, was it because;
- we defer to the batch size assumptions in our ERP/MRP system?
- we want to keep people “busy”?
- of a “dead-cert” sales forecast?
- we worked from a persona and not knowledge of real customer needs?
- of an important utilisation target?
- we want to maintain customer service levels?
- we push not pull?
- We haven’t really embraced SMED?
And many other possible reasons. For each one of the reasons you find there will almost certainly be a simple to understand but challenging lean remedy for it. Challenging in the sense that if you are truly attacking a long-standing chronic loss it won’t necessarily be painless and will probably require a change in design and thinking for it to work. For sometimes the chronic loss is really only there because you or your leaders choose not to see it.