Busting Paradigms with Principles – Part One
“Where is the Life we have lost in living?
Where is the wisdom that we have lost in knowledge?
Where is the knowledge that we have lost in information?“
T.S. Eliot, The Rock
Experiencing the uncomfortable “valley of despair”
In the age of “big data”, information and, paradoxically, complexity there is a fundamental truth in Eliot’s poem, “The Rock”. Lean leaders and managers often end up with knowledge lost in information, tools or models. You must aim to challenge previous paradigms about leadership, lean, TPS and systems. Unlearning and learning brings (obvious) contradictions and disruption. You must encourage a curiosity and desire to view previously solid frameworks or knowledge from totally new angles. A successful workshop wee, for me, would be one that leaves the group uncomfortable and questioning their own, previously solid, understanding of leadership, lean, TPS and systems. It is sometimes good to feel “consciously incompetent” (again).
Data-Information-Knowledge-Wisdom (DIKW)
In her in-depth analysis from 2007 Jennifer Rowley of Bangor Business School, University of Wales, identified “The Rock” as the possible origin of the Data-Information-Knowledge-Wisdom (DIKW) hierarchy. In the DIKW hierarchy the progression to wisdom is characterised by increasing levels of both understanding and context. One needs to be in balance with the other to advance through the hierarchy.
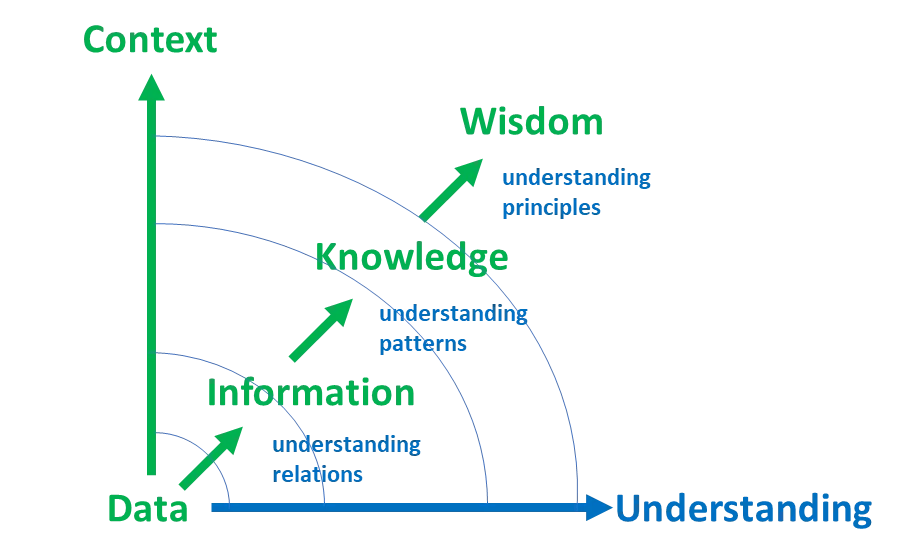
Adapted from Ackoff, R. L., “From Data to Wisdom”, Journal of Applied Systems Analysis, Volume 16, 1989 p 3-9.
Knowledge needs both Context and Understanding
Often we find that many people who have experienced lean and improvement over the last 20 years or so have really only experienced a tool-based lean or improvement approach full of fragile 5S and Rapid Improvement Events. This is “paint-by-numbers” and is founded in memorising information, acronyms and the standard “lean” sequence. We can even “prove” how good our memory is by gaining an ever-growing number of certificates or coloured belts. Whilst this might add a line to our CV or Linkedin profile it doesn’t necessarily add knowledge or beyond that, wisdom. Often when we start from standards and tools the contextual information we need is lost along with meaning and knowledge. Prof. John Seddon asks us to use various simple but powerful questions to test the usefulness of a chosen tool before simply just applying it, such as:
- What problem is it trying to solve?
- Do you have that same problem?
Fundamentally, Prof. John Seddon and other similar thought-leaders advise that we should only look to replicate TPS in our organisations if we have the same problems as or find ourselves in the same situation that once confronted Toyota. Context and situational awareness are critical.
Got a New Hammer – You See Every Problem as a Nail
The uncomfortable feeling that we want our clients to experience comes about when they realise that they too might have applied tools within their own organisations without sufficiently understanding the context, circumstance or system. Let’s take an example to make it real. Say that in the past you have run a quick changeover workshop on a machine with excess capacity. What problem is the SMED workshop trying to solve? Did you do it to reduce labour inefficiency, reduce “waste”, reduce the batch size or increase capacity? On many occasions this improvement would have just resulted in even more spare capacity and a pile of inventory in front of the next process. With hindsight (learning) we see it was potentially the wrong thing to do. The knowledge that we have acquired is an equal balance of context and understanding. Of course, we could just stick at the information level and apply our new tool to all the other machines.